继续调试
换上了淘宝上新买的喉管、铁氟龙送料管和送料管接头,出丝就正常了。另外,才知道铁氟龙管还有透明和乳白色两种,材质有点不同的,据说乳白色的更好。
第一次打印一个小方块出来,兴奋得不得了。
虽然能打印东西出来了,但实际上调试的磨难才刚刚开始。
打印校准立方体,发现问题 X、Y 尺寸有百分之几的偏差,直角不够垂直,最重要的问题是底部刚开始的几层错位严重,每层都比下面一层错位一两毫米。
出料堆积
观察发现打印路径上有很多短边和转折的时候,会在端点上有出料堆积,堆多了造成打上一层时打印头刮碰。以为是这个原因造成的错位。到百度“3d打印”贴吧上问人,别人指出了几个可能问题:
- 堆积材料因为冷却不够
- 打印头漏料
- 错位是因为步进电机丢步
一检查,果然打印头有漏料。因为加热铝块和铜喷嘴的热膨胀系数不同,常温下拧紧的喷嘴高温下变得很松动,需要加热后再拧紧。
又加了小风扇在旁边吹打印模型,加速降温。但这个不是主要原因。在切片软件中降低挤出系数减少出料量,就没有堆积现象了。
电机丢步的评论我没有重视。(那时我还不知道怎样的现象是丢步,后来才发现其实这个才是真正原因。贴吧的人气很低,问问题很多天都没什么回应,但上面有些人确实有经验。)
可是,问题依然存在。
框架偏差
仔细观察打印机框架,感觉立柱有一点点倾斜。用垂线测量了一下,确实是往一个方向出现了剪切位移。
框架用很多颗螺丝拧紧,型材插进角件中,有一点裕度,螺丝一压紧,难以控制它不倾斜。感觉要调正很困难,把解决的方向放在打印床上,想把玻璃打印床的固定螺丝换成弹簧可调节的,通过调整平面去让它与立柱垂直。
本来都要买调平螺丝了,晚上尝试了一下把打印机横放,底座的螺丝拧松一半,一个个直角来调整:先把螺丝拧到半紧,但用力还能稍微掰得动的程度,用直角尺量着立柱和平台的角度慢慢调整,直到把两根铝型材调整到正交,调好一处上紧一处的螺丝,一共6组。居然最后给调准了,用垂线测量基本上没有误差。
可是,这并不是导致层错位的原因。
自动调平
打印小立方体时,打印头只在打印平面的中心附近移动。尝试打大面积的校准模型,发现打印头在某些边缘位置会刮到打印床玻璃上,觉得是调平还有问题。
手工调平效率太低了,靠抽纸的方式来判断也不够准确。本来打算能自己打零件,才打印一个自动调平开关的安装座的,现在打印机的误差太大根本不能打零件。
于是买了一个压力传感器,无需安装,需要用时套到喷嘴上就行,当喷嘴下压到打印床上,传感器上下两片触片就会闭合。事实证明,这种传感器虽然贵一点,但绝对值得:
- 使用方便,套上去就行
- 与喷嘴没有高度差,没有水平偏差,不需要测量和在固件中设置位移
- 不需要在效应器上额外安装东西,不会增加重量
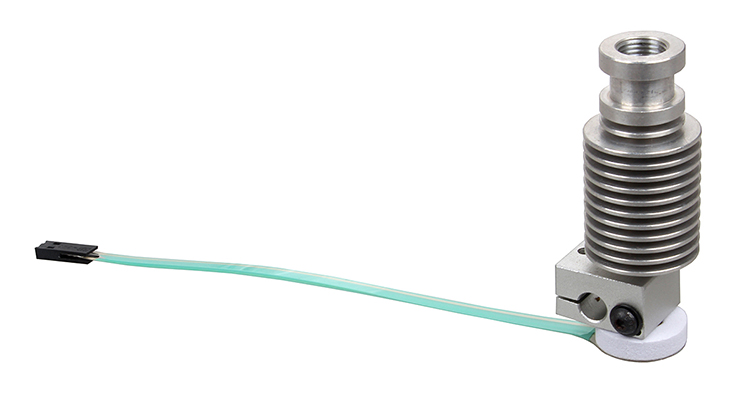
另外也怀疑endstop的机械微动开关触发不准确,买了光电阻挡触发开关,不过后来也没有装上。
有了自动调平功能,看着打印头哒哒哒的敲打着玻璃板,十几个测量点反复测多轮,手工根本做不到,效率天上地下之差。
可是,自动调平之后,打印出来的立方体变形得更加厉害了,从底到顶都是歪的。
电机失步
有了压力传感器,尝试用 G30 指令做单次Z probe,发现连测几次结果都不一样,似乎是打印头接触玻璃板后没有立即停下来,造成错位了。修改固件,降低 Z probe 速度,慢动作之下就看出来了:打印头接触玻璃板后,水平滑动了一段距离才抬起——本来应该一探到玻璃板,开关触发,就马上抬起来的。以为是压力传感器不够敏感,试了用 M119 指令查看状态,手指头轻轻一压传感器,状态就变化了,也不是传感器问题。
而且,观察到这个滑行现象在探测点靠近B柱的时候特别明显,而在其他位置就不会发生。
百思不得其解,在百度贴吧和 3dprinting.stackexchange.com 上提问,都没有人回答。(贴吧在半个月后有高人指出问题,可那时我已经解决了)
后来试试用手阻挡滑块的运动,感受一下电机的力度。电机的力度蛮大的,我才明白为什么刚开始出料堆积造成打印头刮碰时,别人都没当这是原因——材料被打印头刮碰时已经被加热软化,所产生的阻力对电机来说算不上什么。而试到B柱时,电机的力度不足,手稍微用力阻挡就会打滑——原来这个就叫做电机的失步!
没有亲自尝试体会,没法完全理解别人的经验。
更换了步进电机,重新自动调平,4点测量后就已经准确校准了,后面的25点、100点测量都是一个迭代就收敛。到此为止,打印功能完全正常。
完善
接下来,是一些完善的工作。
模型散热
E3D v6 挤出头配了散热风扇,只是给挤出头散热的,不吹打印工件,所以我用个充电宝带个小米风扇在旁边吹。这样不是太方便,而且风扇距离太远也无法做到材料一挤出喷嘴就能立即冷却固化。看别人的设计,有些是在打印头旁边加挂一个风扇吹工件,看起来臃肿占地方,也增加重量。
在 Thingiverse 上见到一个二合一的风扇风道设计,一个风扇分出两个风道,分别给挤出头散热和吹向喷嘴周边。
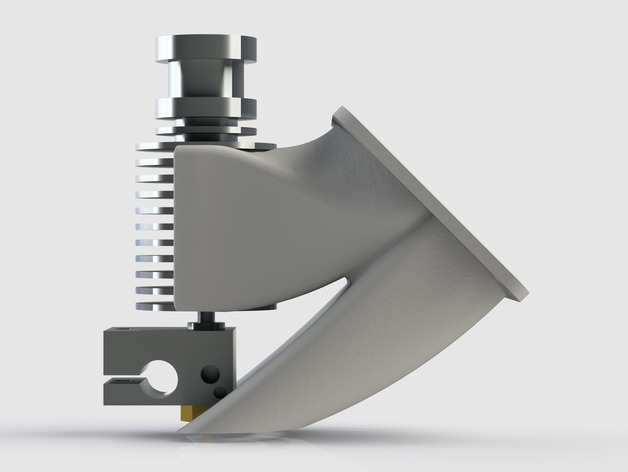
制作了一个,感觉不够理想:
- 风扇凸出太多,打印头运动到边缘时会碰撞立柱,减少了可打印范围半径
- PLA材料弹性不够,夹在挤出头上可能会不够牢固
想到改进的方向:
- 外形紧凑,尽可能少凸出于效应器投影面:减少风扇倾角,尽量垂直放置;缩短风道长度
- 重用原来 E3D v6 配套的塑料风扇座,那个比较牢固
重新设计了一个,也发布到 Thingiverse 上了:https://www.thingiverse.com/thing:2781523
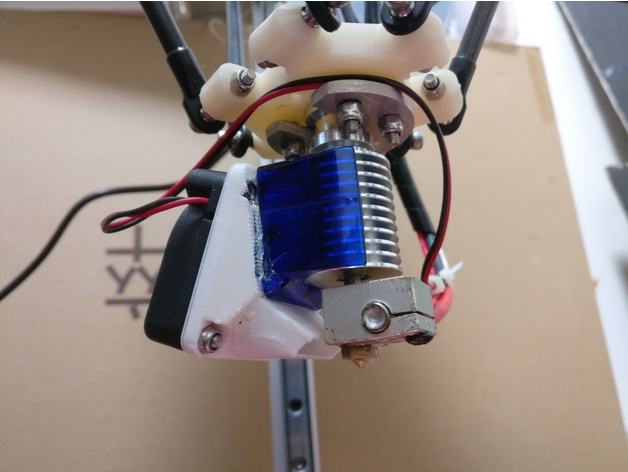
挤出机导管
用的是 MK8 远程挤出机,铝合金材质很结实,回抽的效果也不差,但设计还说不上很完美:
- 虽然进料孔、出料孔和齿轮边缘在一条直线上,但由于挤丝的一边是平的挤丝齿轮一边是带槽的堕轮,丝受压就歪向带槽的一方了,造成很难将丝插入出料孔。在打印前穿丝还可以用小螺丝刀拨着方向慢慢试,在打印过程中想接丝就没可能做到了。
- 换丝时即使按下杠杠松开压轮,丝线还是会摩擦挤丝齿轮。但这也不算什么问题了。
看到有人用铁氟龙管替换堕轮,让整个进丝通道都在管中,我也试了一下。可是打印出来的工件很疏松,送料不足的样子,就装回堕轮了。后来再想,也许将挤压丝线的压力调大能有改善。
后来在出料孔前加了一小截铁氟龙导管,虽然还是做不到不靠手工辅助就能准确插入管中,但起码好操作一些了,打印过程中也能够接上另一段丝线。
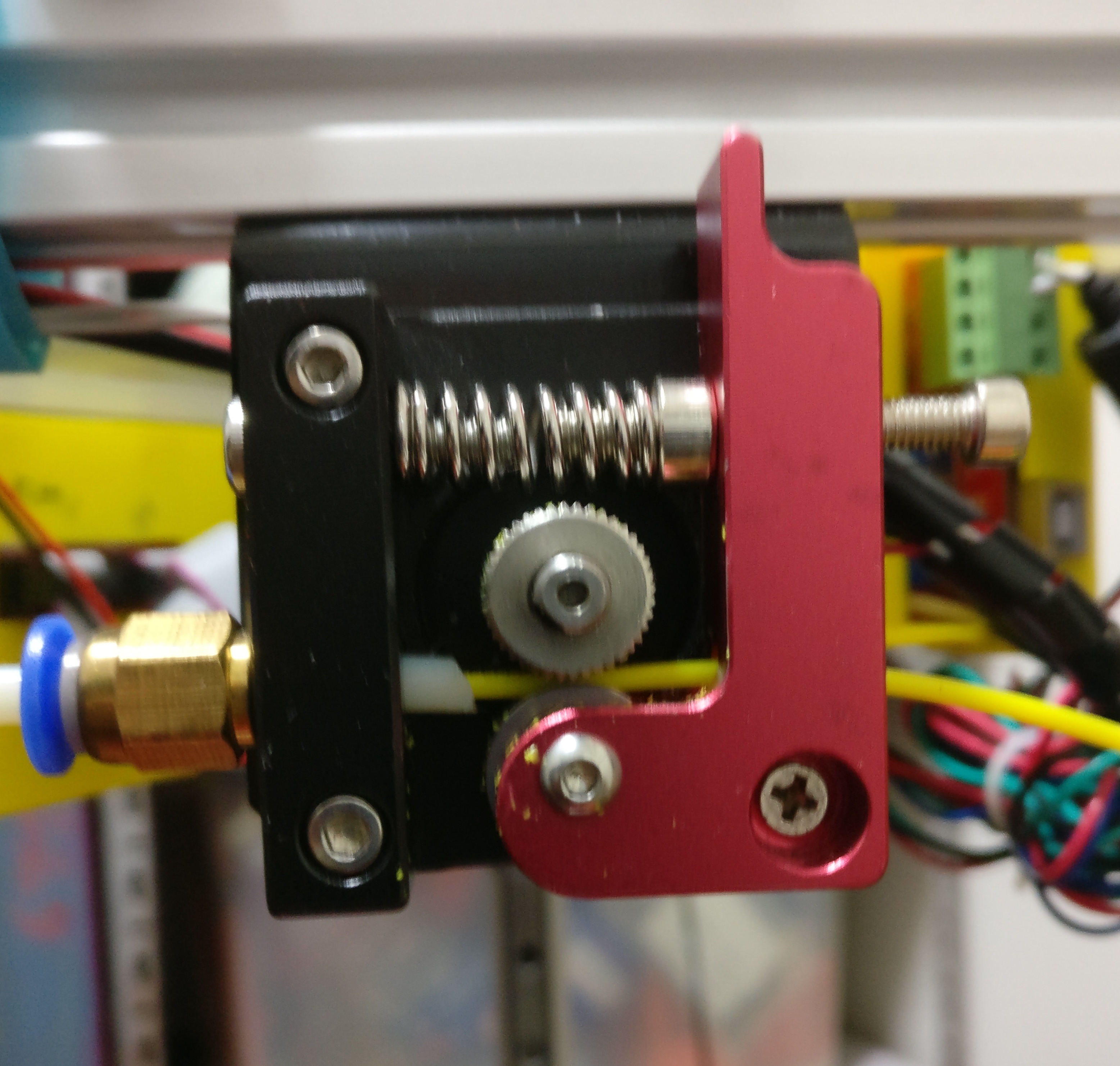
电路板外壳
电路板裸露会比较脆弱,得做个外壳装起来。
一个LCD控制器的外壳,一个 RAMPS+Arduino的外壳,搞了好几天才弄好。最大的感受是:设计不难,建模不难,最麻烦的事情是怎么把尺寸测量准确。知道为什么说 3D 打印机是工业设计的好辅助工具了,电脑做的模型还是要做个真实样品出来才能验证,根据实物再做修改调整。如果没有快速成型工具,直接出模具,很可能就废了
做的各种零件,基本上都要打印两三次甚至更多才能最终确定设计。这种FDM 3D打印的速度其实很慢,半边外壳就要打印一个多小时。节省时间的方法是对于设计不确定、可能出问题的复杂的部分,先打印一块局部出来。
各种各样的测试品一堆:
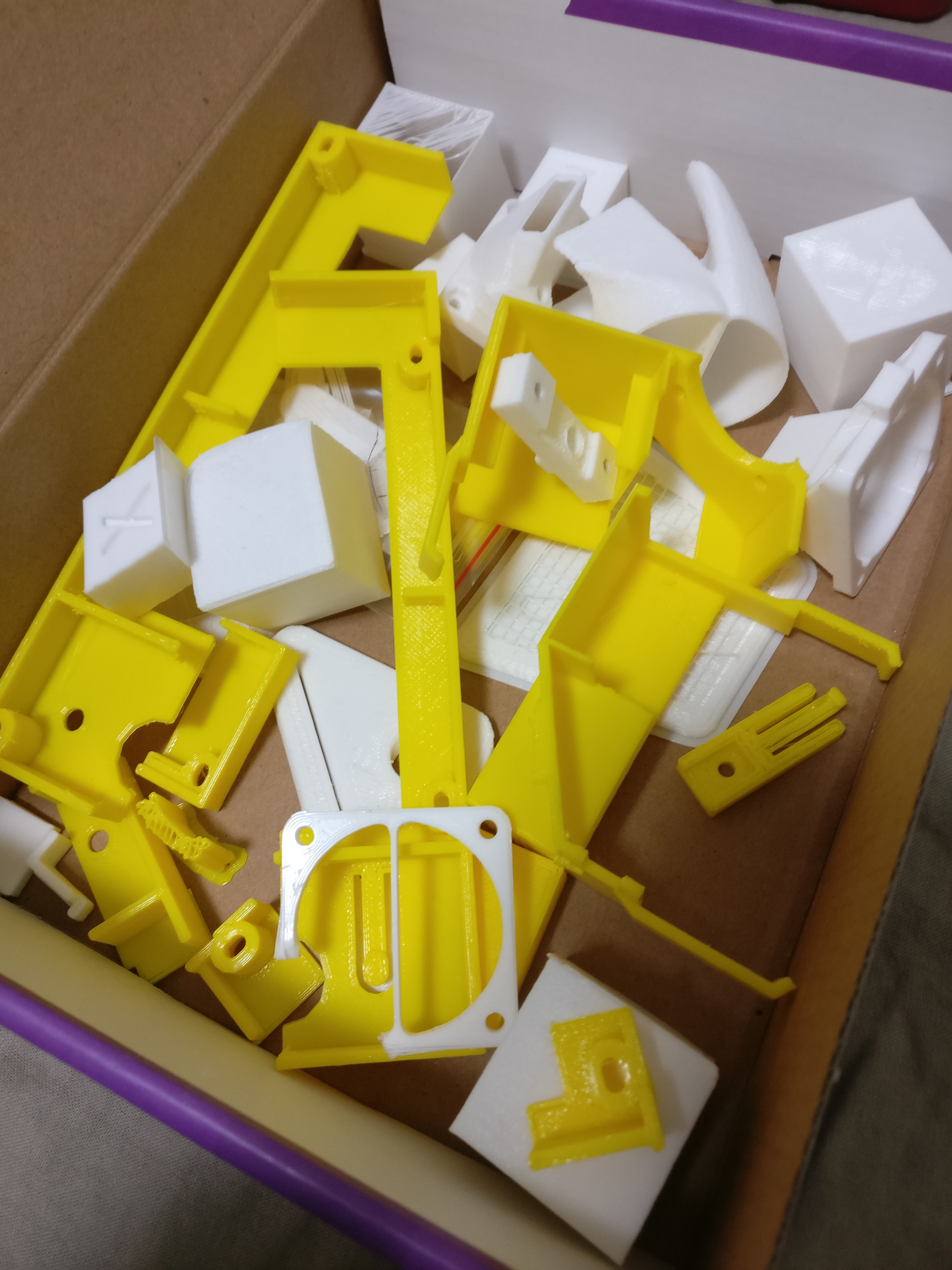
Kossel Mini 原来的设计里,电路板是放在框架的上方的。Delta结构打印机由于悬臂,上部空间浪费很多。于是我将LCD、Arduino和挤出机都改成挂在框架横梁下面,减少了整机高度,另外处于铝合金框架的保护之中,搬动、摆放也会安全一些。
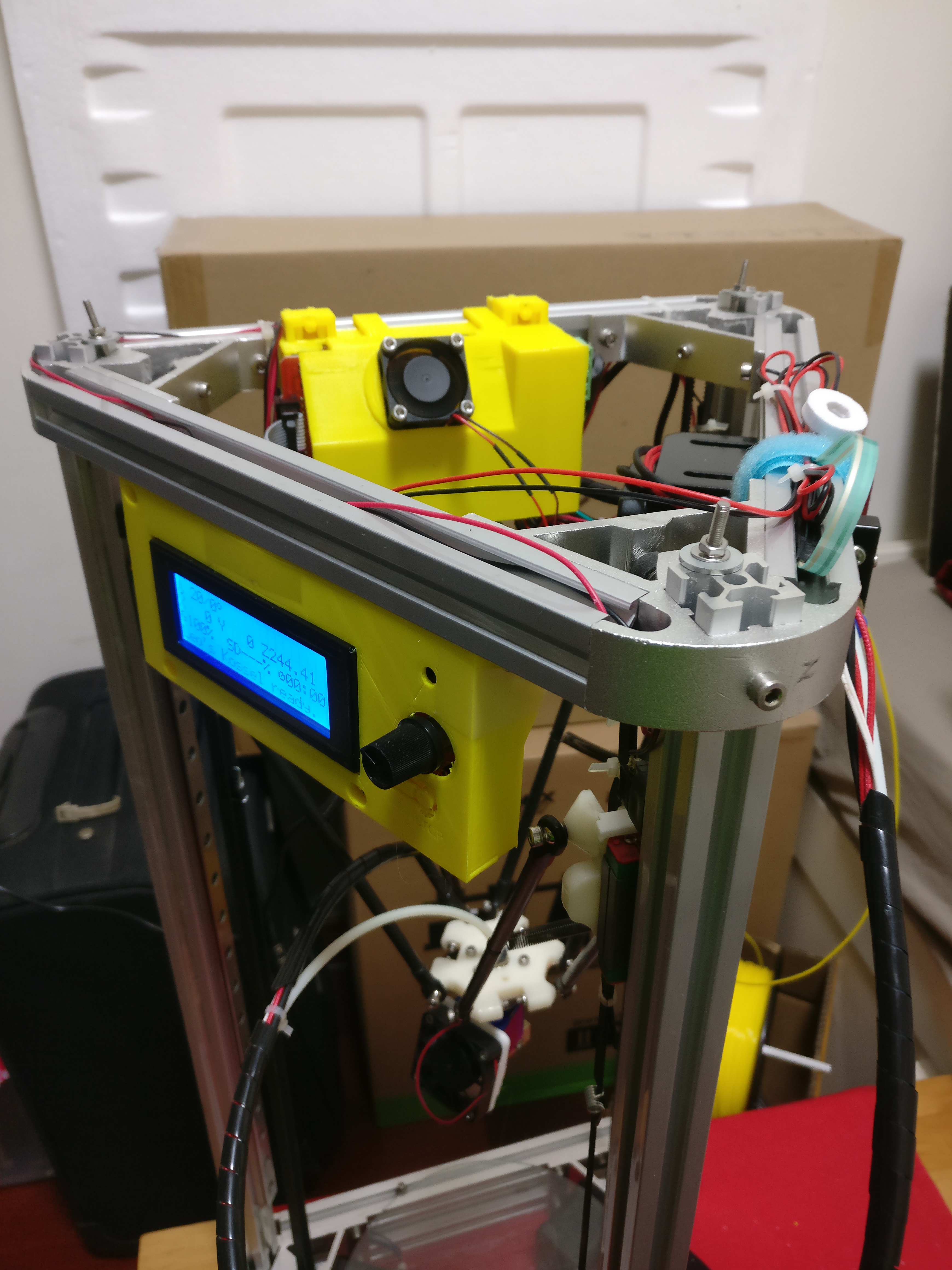
RAMPS+Arduino的外壳的设计放在 Thingiverse上:https://www.thingiverse.com/thing:2806140 。LCD控制器我的做得不如别人的好,就没有放上去。
这个3D打印机设计全过程涉及的资料,包括安装手册、参考资料、物料清单(BOM)和淘宝购买链接、打印模型源文件、照片都存放在 https://github.com/aleung/kosselprinter